BARITE SORTING
Barite sorting machine
BARITE SORTING MACHINE
What is Barite sorting?
A barite sorting machine is specialized equipment used in mining operations to separate barite-bearing ore from waste material. It employs various technologies such as sensors, optics, and AI algorithms to efficiently and accurately identify and separate barite ore based on specific characteristics like density, color, and chemical composition. This sorting process enhances mining efficiency, reduces waste, and maximizes the recovery of valuable barite minerals.

Ore sorting is a process used in mining operations to separate valuable minerals from waste material based on their physical or chemical properties. The technique relies on various technologies and principles to achieve efficient separation. Below is a detailed explanation of the principles behind ore sorting:
- Sensor Technology: Ore sorting utilizes advanced sensor technologies to detect and measure specific properties of the ore particles. These sensors can include:
- X-ray Transmission (XRT): XRT sensors use the differential absorption of X-rays by different materials to identify and separate ores based on their atomic density and composition. Dense minerals absorb more X-rays than lighter ones, allowing for differentiation.
- Near Infrared (NIR) Spectroscopy: NIR sensors analyze the reflectance or absorbance of near-infrared light by minerals. Different minerals have unique spectral signatures, enabling their identification and sorting.
- Color Cameras: Color cameras capture images of the ore particles based on their color and texture. Image analysis algorithms are then used to classify and sort the particles accordingly.
- Particle Recognition and Classification Algorithms: Once the sensor data is collected, sophisticated algorithms are employed to analyze and classify the ore particles based on the information provided by the sensors. These algorithms can differentiate between valuable minerals, waste material, and gangue based on their physical and chemical properties.
- High-Speed Actuators and Sorting Mechanisms: After classification, high-speed actuators and sorting mechanisms are used to physically separate the ore particles based on their classification. These mechanisms can include conveyor belts, air jets, mechanical paddles, or electromagnets, depending on the specific sorting technology employed.
- Feedback Loop and Optimization: Ore sorting systems often incorporate a feedback loop mechanism wherein the performance of the sorting process is continuously monitored and adjusted based on real-time data. This optimization ensures maximum efficiency and accuracy in separating valuable minerals from waste material.
- Integration with Mining Operations: Ore sorting technologies are integrated into existing mining operations, either as standalone units or as part of a larger processing plant. The sorted ore particles are then further processed through crushing, grinding, and other beneficiation techniques to extract the valuable minerals.
Overall, ore sorting technologies offer significant benefits to mining operations, including increased productivity, reduced energy and water consumption, and improved overall ore recovery rates. By leveraging advanced sensor technologies and intelligent algorithms, ore sorting enables more efficient and sustainable mineral processing practices.
1. Mining Industry:
- Precious Metal Mining: Ore sorting is widely used in gold, silver, and platinum mining to separate high-grade ore from lower-grade material, increasing overall efficiency and reducing processing costs.
- Base Metal Mining: Copper, zinc, and lead mines use ore sorting to improve the quality of ore feed, leading to higher metal recovery rates and reduced environmental impact.
2. Mineral Processing:
- Industrial Minerals: Ore sorting is applied in the processing of industrial minerals such as limestone, talc, and quartz to remove impurities and enhance product quality.
- Construction Materials: Sorting is used in the production of construction materials like aggregates and dimension stones to separate out contaminants and ensure uniformity in final products.
3. Recycling Industry:
- Metal Recycling: Ore sorting technologies are used in metal recycling facilities to separate different types of metals from mixed waste streams, improving recycling rates and reducing landfill waste.
- Plastic Recycling: Optical sorting technologies can be applied in plastic recycling to separate different types of plastics based on their resin type, color, and density.
4. Environmental Remediation:
- Mine Waste Reclamation: Ore sorting can be used in mine waste reclamation projects to separate valuable minerals from waste rock, reducing the environmental impact of mining activities.
- Landfill Remediation: Sorting technologies can help recover valuable materials from landfill sites, reducing the volume of waste and recovering resources for reuse.
Ore sorting technologies play a crucial role in various industries, enabling efficient resource utilization, reducing waste, and improving the quality of end products.
1. Sensor-Based Sorting:
Sensor-based sorting technologies rely on various sensors to detect specific properties of ore particles. These sensors include:
- X-ray Transmission (XRT): Utilizes differential absorption of X-rays by different materials to identify and separate ores based on atomic density and composition.
- Near Infrared (NIR) Spectroscopy: Analyzes reflectance or absorbance of near-infrared light by minerals to identify and sort them based on their spectral signatures.
- Color Cameras: Capture images of ore particles based on color and texture, utilizing image analysis algorithms for classification and sorting.
2. Gravity-Based Sorting:
Gravity-based sorting technologies rely on the principle of density to separate ore particles. These include:
- Dense Media Separation (DMS): Utilizes a dense medium such as ferrosilicon or magnetite to create a sink-float separation based on density differences.
- Gravity Concentration: Utilizes the force of gravity to separate ore particles based on differences in density, typically applied in gold, tin, and tungsten processing.
3. Magnetic Sorting:
Magnetic sorting technologies utilize magnetic properties of minerals to separate them from gangue. These include:
- Magnetic Separators: Use magnetic fields to attract and separate ferromagnetic minerals from non-magnetic materials.
- High-Gradient Magnetic Separation (HGMS): Utilizes a magnetic matrix to capture fine magnetic particles, offering high selectivity and efficiency.
4. Electrical Sorting:
Electrical sorting technologies exploit differences in electrical conductivity or electrostatic properties of minerals. These include:
- Electrostatic Separation: Utilizes differences in electrical conductivity to separate conductive and non-conductive minerals.
- Triboelectric Separation: Relies on differences in surface charging properties to separate particles based on their triboelectric characteristics.
5. Hybrid Sorting:
Hybrid sorting technologies combine multiple sorting principles for enhanced efficiency and effectiveness. These may include combinations of sensor-based, gravity-based, magnetic, and electrical sorting techniques.
Ore sorting technologies offer versatile solutions for separating valuable minerals from waste material, contributing to increased efficiency and sustainability in mining and mineral processing operations.
Ore sorting technology has undergone significant advancements in recent years, and its future looks promising with several emerging trends:
1. Advancements in Sensor Technology:
Continuous advancements in sensor technology, including X-ray transmission (XRT), near-infrared (NIR) spectroscopy, and hyperspectral imaging, are enhancing the capabilities and efficiency of ore sorting systems. These sensors are becoming more sensitive, accurate, and cost-effective, enabling finer particle size sorting and improved mineral identification.
2. Integration of Artificial Intelligence (AI) and Machine Learning:
The integration of AI and machine learning algorithms into ore sorting systems is revolutionizing the way minerals are processed. These technologies enable real-time data analysis, predictive modeling, and adaptive control, optimizing sorting performance and increasing overall efficiency.
3. Enhanced Resource Recovery and Sustainability:
Ore sorting technologies are increasingly being employed to recover valuable minerals from low-grade or previously uneconomic deposits. This trend contributes to sustainable mining practices by reducing waste generation, energy consumption, and environmental impact while maximizing resource utilization and ore recovery rates.
4. Application Diversification:
There is a growing trend towards the diversification of ore sorting applications beyond traditional mining and mineral processing sectors. Ore sorting technologies are being applied in industries such as recycling, environmental remediation, and food processing, offering new opportunities for resource recovery and waste management.
5. Development of Modular and Mobile Solutions:
Modular and mobile ore sorting solutions are gaining popularity due to their flexibility, scalability, and cost-effectiveness. These compact systems can be easily deployed in remote or temporary mining operations, providing rapid deployment and quick return on investment.
6. Focus on Sustainable Mining Practices:
There is an increasing emphasis on integrating ore sorting technologies into sustainable mining practices. By improving resource efficiency, reducing water and energy consumption, and minimizing environmental impact, ore sorting contributes to the transition towards more environmentally and socially responsible mining operations.
The future of ore sorting technology holds immense potential for driving innovation, efficiency, and sustainability in the mining and mineral processing industries. Continued research and development efforts, along with collaboration between industry stakeholders, will further enhance the capabilities and adoption of ore sorting technologies worldwide.
Ore sorting technology plays a crucial role in promoting environmental sustainability and fostering the principles of sustainable development in the mining and mineral processing industries:
1. Resource Efficiency:
Ore sorting enables more efficient use of resources by targeting high-grade ore deposits and separating valuable minerals from waste material. This results in reduced ore processing volumes, lower energy consumption, and minimized environmental footprint associated with mining operations.
2. Waste Reduction:
By selectively separating valuable minerals from low-grade or uneconomic ore material, ore sorting helps in reducing the generation of mining waste and tailings. This contributes to mitigating environmental pollution, land degradation, and the risk of harmful environmental incidents such as tailings dam failures.
3. Energy and Water Conservation:
Ore sorting systems are designed to operate with high efficiency, requiring less energy and water compared to conventional ore processing methods. The reduction in energy and water consumption not only lowers operating costs but also minimizes the environmental impact associated with resource extraction and processing.
4. Reduced Environmental Footprint:
The adoption of ore sorting technologies results in a smaller environmental footprint for mining operations. By optimizing resource utilization, reducing waste generation, and minimizing the use of chemicals and reagents, ore sorting contributes to overall environmental sustainability and compliance with environmental regulations.
5. Rehabilitation and Reclamation:
Ore sorting can aid in the rehabilitation and reclamation of mining sites by facilitating the recovery of valuable minerals from waste materials and tailings. This promotes the restoration of disturbed landscapes and ecosystems, fostering long-term environmental stewardship and community engagement.
6. Support for Sustainable Development Goals (SDGs):
Ore sorting aligns with several Sustainable Development Goals (SDGs) outlined by the United Nations, including Goal 12 (Responsible Consumption and Production) and Goal 15 (Life on Land). By promoting responsible resource management, environmental protection, and social welfare, ore sorting contributes to achieving sustainable development objectives at both local and global levels.
Overall, ore sorting technology represents a sustainable solution for enhancing resource efficiency, reducing environmental impact, and promoting responsible mining practices. Continued investment in research, innovation, and technology adoption is essential for maximizing the environmental and sustainability benefits of ore sorting in the mining industry.
Ore sorting machines have become integral equipment in the global mining and mineral processing industries, contributing to improved efficiency and resource utilization.
Market Size:
The global ore sorting machine market is huge and growing rapidly. This growth is driven by the increasing adoption of advanced sorting technologies to enhance ore processing efficiency, reduce operational costs, and improve resource recovery rates.
Key Drivers:
Several factors are driving the growth of the ore sorting machine market globally:
- Rising demand for high-quality minerals and metals in various industries such as construction, automotive, electronics, and renewable energy.
- Growing focus on sustainable mining practices and environmental stewardship, leading to the adoption of technologies that minimize waste generation and environmental impact.
- Advancements in sensor technology, artificial intelligence, and machine learning, enabling more accurate and efficient sorting of ore particles.
- Increasing investments in mining automation and digitalization to optimize operational processes and improve overall productivity.
Regional Analysis:
The market for ore sorting machines is geographically segmented into regions including North America, Europe, Asia Pacific, Latin America, and the Middle East & Africa. North America and Europe are anticipated to hold significant market shares owing to established mining industries and stringent environmental regulations. However, the Asia Pacific region is expected to witness the highest growth rate during the forecast period, driven by rapid industrialization and infrastructure development in countries like China, India, and Australia.
Future Outlook:
The future outlook for the ore sorting machine market is promising, with sustained growth expected driven by technological advancements, increasing mining activities, and the growing demand for sustainable mineral processing solutions. The market is likely to witness the introduction of new sorting machine models, expansion into emerging markets, and greater emphasis on product efficiency and environmental sustainability.
In conclusion, the ore sorting machine market presents significant growth opportunities for industry players, driven by the need for efficient ore processing solutions and the ongoing transition towards sustainable mining practices worldwide.
Main Methods of Ore Sorting
An essential step in mining operations to improve efficiency and reduce waste
- Gravity Concentration: Utilizes the difference in density between minerals to separate them.
- Flotation: Relies on the selective attachment of certain chemicals to minerals, allowing them to float to the surface.
- Magnetic Separation: Exploits the magnetic properties of minerals to separate them.
- Sensor-Based Sorting: Uses sensors to detect differences in properties such as color, density, and conductivity for sorting.
- Optical Sorting: Relies on optical properties such as color and shape for sorting.
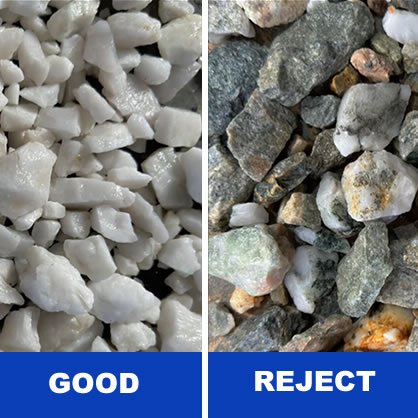
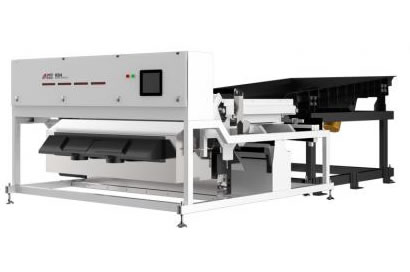
Large Particle Ore Sorting Machine
Our large particle ore sorting machine is engineered to efficiently handle bulk materials such as coal, limestone, and iron ore. With its capability to process particles ranging from several centimeters to decimeters in size, it excels in mining operations dealing with large-sized ores. Whether sorting coal for power generation or separating iron ore for steel production, our machine ensures optimal efficiency and accuracy in identifying valuable ores amidst bulk materials.
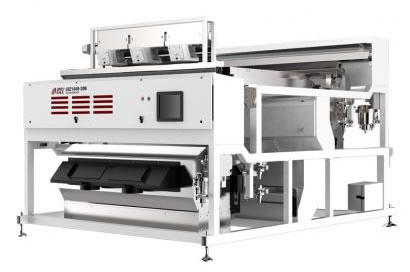
Medium Particle Ore Sorting Machine
Tailored for precision sorting of medium-sized particles, our medium particle ore sorting machine is the go-to solution for processing base metals, precious metals, and industrial minerals. Operating with particle sizes ranging from millimeters to centimeters, it offers unparalleled sorting accuracy and efficiency. Whether sorting copper, zinc, or gold ores, our machine delivers consistent results, enabling miners to achieve desired product quality and grade with confidence.
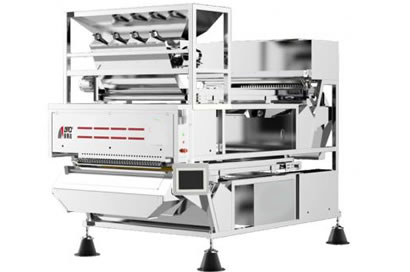
Small Particle Ore Sorting Machine
For applications requiring fine particle sorting, our small particle ore sorting machine is the perfect choice. Designed to handle particles from millimeters to micrometers in size, it excels in processing fine-grained ores and industrial minerals. Whether separating tin, tungsten, or rare earth elements, our machine ensures precise sorting, enabling miners to recover valuable minerals efficiently and effectively.

Powder Ore Sorting Machine
Our powder ore sorting machine is tailored for sorting ultra-fine particles, making it indispensable for processing fine-grained ores, industrial minerals, and mineral powders used in various industries. Operating with particle sizes ranging from micrometers to millimeters, it offers unmatched sorting accuracy and efficiency. Whether sorting titanium, barite, or graphite powders, our machine delivers superior performance, ensuring optimal recovery of valuable minerals in every application.
To improve the ore grade and quality?
We are fully committed to delivering the most advanced ore sorting solutions available worldwide. Our team of engineers stands ready to provide comprehensive technical support whenever you need it. Feel free to contact us at any time!
CALL US